Discover the versatile potential of Fly Ash: a sustainable by-product rich in cementitious properties, revolutionizing construction materials and infrastructure projects worldwide. Harnessing its resilience and adaptability, Fly Ash empowers sustainable solutions for diverse applications, from building materials to environmental remediation.
Coal ash particles undergo collection via electric precipitators and subsequent melting during combustion, transforming into vitreous, spherical forms suspended in the hot gases.
Known as Floating Fly Ash (FFA), these hollow, lightweight spheres boast a grayish-white hue, thin walls, and a closed, smooth surface ideal for thermal insulation applications. With bulk densities ranging from heavy to light, and diameters around 0.1 mm, FFA exhibits low thermal conductivity, high density, and remarkable gas barrier properties, making it a preferred choice for insulating materials in various industrial settings.
Primarily comprised of silica and aluminum oxide, FFA showcases fine grain structure, exceptional strength, wear resistance, and high-temperature resilience, rendering it indispensable in the refractory raw material industries for diverse applications demanding superior insulation and durability.
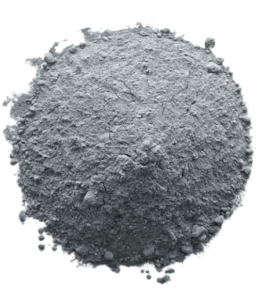
Applications of Fly ash
- Fly ash, a by-product of coal-fired power plants, offers a valuable alternative to conventional clinker due to its high cementitious content, making it suitable for various product applications.
- Rich in silicon and aluminum, fly ash derived from pulverized coal combustion serves as a versatile resource for construction materials, contributing to sustainable building practices.
- Embraced by the Federal Highway Administration, fly ash finds utility in embankment and mine fill projects, showcasing its increasing recognition and versatility in infrastructure development.
- Derived from cement kilns, fly ash exhibits remarkable porosity and compression resistance, delivering exceptional bearing strength and compaction qualities essential for robust construction projects.
Composition :
Components | 90% |
Silica | 1 |
Aluminia | 2 |
Inert gases | >4 |