Cenospheres, by-products of coal combustion, are lightweight, hollow spheres comprised of alumina and silica, offering versatility in various applications. Their color ranges from grey to nearly white, with a density of 0.4 – 0.8 g/cm3, providing buoyancy and enhancing workability.
Functioning like miniature ball bearings, cenospheres improve material flow, reduce shrinkage, and enhance isotropic properties while decreasing the demand for resins, binders, or water due to their low oil absorption and high packing efficiency. These rigid, waterproof, and inert spheres also possess excellent thermal insulation properties, making them ideal for producing lightweight materials with superior heat resistance at an economical cost. Utilizing the advantages of cenospheres can significantly reduce the weight of formulated products while maintaining structural integrity.
Benefits
The spherical nature of Cenospheres enhances material flow and ensures uniform dispersion in various applications, making them invaluable in industries such as oil drilling, paints, and fillers. Widely recognized as Glass Beads, Hollow Ceramic Spheres, or Microspheres, they boast consistent properties akin to sphered products, offering controlled size, low specific gravity, and high compression.
Primarily utilized to reduce the weight of plastics, rubbers, cements, and resins, Cenospheres also serve as filler lubricants in oil drilling operations, enduring high heat and stress conditions down the borehole. Their versatility extends to applications like oil well cementing and mud putty formulation, contributing to improved performance and efficiency.
Initially adopted in the United States as extenders for plastic compounds, Cenospheres have demonstrated compatibility with plastisols, thermoplastics, and latex, further cementing their role as multifunctional additives in diverse industrial settings.
How they are produced?
Cenospheres are typically produced as a byproduct of coal combustion in thermal power plants. During the burning process, when coal is subjected to high temperatures (typically between 1,500 to 1,750 °C or 2,730 to 3,180 °F), the mineral components of the coal, such as alumina and silica, melt and fuse together.
Within the combustion chamber, these molten mineral particles undergo complex physical and chemical transformations. As the temperature cools down, small, hollow ceramic spheres known as cenospheres form within the fly ash.
These cenospheres are lightweight and inert, containing trapped air or inert gases. Once the combustion process is complete, the fly ash, along with the cenospheres, is collected using filtration systems such as electrostatic precipitators or bag filters.
After collection, the cenospheres are separated from the fly ash through various mechanical and density-based separation processes. The resulting cenospheres are then processed further, including drying and sieving, to produce cenosphere products of desired size and quality suitable for various industrial applications.
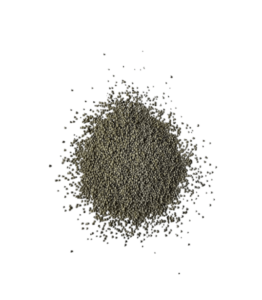
Manufacturing Process
Cenospheres are typically manufactured as a byproduct of coal combustion in thermal power plants. Here’s an overview of the manufacturing process:
Coal Combustion: The process begins with the burning of coal in a thermal power plant boiler. During combustion, the mineral components of coal, such as alumina and silica, melt at high temperatures.
Formation of Cenospheres: As the melted mineral particles cool down, they solidify and form small, hollow ceramic spheres known as cenospheres. These cenospheres are lightweight and typically filled with trapped air or inert gases.
Collection: After the combustion process, the fly ash containing cenospheres is collected using filtration systems like electrostatic precipitators or bag filters. These systems capture the fly ash particles, including the cenospheres, before they are released into the atmosphere.
Separation: The collected fly ash is then processed to separate the cenospheres from other ash components. This separation process often involves mechanical and density-based techniques to isolate the lightweight cenospheres from the heavier ash particles.
Processing: Once separated, the cenospheres undergo further processing steps such as drying, sieving, and quality control measures. Drying helps remove any remaining moisture, while sieving ensures that cenosphere products meet desired size specifications.
Packaging and Distribution: Finally, the processed cenospheres are packaged and distributed for various industrial applications. These applications include lightweight fillers in concrete, insulation materials, coatings, plastics, and other products that benefit from the unique properties of cenospheres, such as low density and high strength.
Global Demand
The global demand for cenospheres has been steadily increasing due to their versatile properties and wide range of applications across various industries. Here’s an analysis of the factors driving this demand:
Construction Industry: Cenospheres are widely used in the construction industry as lightweight fillers in concrete, providing benefits such as reduced density, improved workability, and enhanced insulation properties. With the growing construction sector worldwide, particularly in developing economies, the demand for cenospheres as a sustainable and cost-effective construction material is on the rise.
Oil and Gas Sector: Cenospheres find extensive use in the oil and gas industry, especially in drilling operations. They are employed as lightweight additives in drilling fluids to improve fluid properties, reduce density, and enhance mud performance. The increasing exploration and drilling activities in both conventional and unconventional oil and gas reserves are driving the demand for cenospheres in this sector.
Automotive and Aerospace Industries: Cenospheres are also utilized in the automotive and aerospace industries for manufacturing lightweight composite materials. These materials offer high strength-to-weight ratios, contributing to fuel efficiency and performance improvements in vehicles and aircraft. With the automotive and aerospace sectors focusing on lightweighting strategies to meet stringent regulations and improve efficiency, the demand for cenospheres as a reinforcement material is expected to grow.
Coatings and Paints: Cenospheres are incorporated into coatings and paints to enhance their properties, such as durability, abrasion resistance, and thermal insulation. The increasing demand for high-performance coatings and paints across various end-use industries, including automotive, construction, and industrial sectors, is driving the demand for cenospheres as an additive.
Growing Awareness of Sustainable Materials: With growing environmental concerns and a shift towards sustainable practices, there is increasing interest in using eco-friendly materials like cenospheres. Cenospheres offer benefits such as resource efficiency, reduced carbon footprint, and waste reduction, making them an attractive choice for industries looking to adopt sustainable solutions.
Overall, the global demand for cenospheres is expected to continue rising, driven by their unique properties and diverse applications across key industries, coupled with increasing awareness of sustainability and environmental considerations.
Composition :
Components | 90% |
loss | <1 |
SiO2 | >55 |
MgO | <1 |
Ai2o3 | >31 |
Ca0 | <2 |
Fe2o3 | <3 |
k2o | >1 |
Tio2 | >1.1 |