Unlock the Potential of Fly Ash: A Sustainable and High-Performance Material
Fly Ash, a versatile by-product with exceptional cementitious properties, is transforming construction and infrastructure projects worldwide. Its strength, durability, and eco-friendly characteristics make it a key component in sustainable building materials and industrial applications.
During coal combustion, fine ash particles are captured through electrostatic precipitators. Some particles undergo vitrification, forming lightweight, hollow spheres suspended in hot gases—commonly referred to as Floating Fly Ash (FFA).
Characterized by a smooth, closed surface and a grayish-white hue, FFA is highly valued for its thermal insulation capabilities. With particle diameters around 0.1 mm and varying bulk densities, it offers low thermal conductivity, high strength, and excellent gas barrier properties, making it an ideal choice for industrial insulation.
Composed primarily of silica and aluminum oxide, FFA possesses a fine grain structure, superior wear resistance, and remarkable heat tolerance. These properties make it an essential material in refractory applications, ensuring durability and efficiency in high-temperature environments.
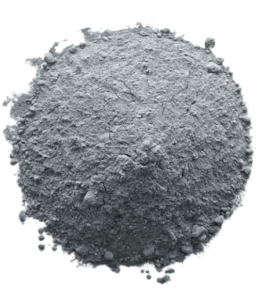
Applications of Fly ash
Fly Ash, a by-product of coal combustion, is an eco-friendly and cost-effective alternative to traditional clinker, owing to its high cementitious properties. Its composition, rich in silicon and aluminum, makes it a valuable resource in construction and infrastructure projects, promoting sustainable building practices.
Widely utilized in road construction, concrete production, and soil stabilization, Fly Ash enhances strength, durability, and workability. Its use in embankment and mine fill projects, recognized by global infrastructure authorities, highlights its growing significance in large-scale developments.
With excellent porosity, compression resistance, and superior load-bearing capacity, Fly Ash contributes to durable, high-performance structures. Its adaptability across diverse applications—from cement manufacturing to geotechnical engineering—continues to drive its demand in modern construction industries.
Composition :
Components | 90% |
Silica | 1 |
Aluminia | 2 |
Inert gases | >4 |